Our service for your needs
Discover our wide range of services
We offer you:
We are happy to support you with our experienced team from your vision to the finished plastic product or assembly. In addition to the many years of experience of our employees, we use computer-aided simulation to reduce potential risks during the development phase.
We provide you with prototypes during the initial phase of your project. Depending on the application, these can be printed or produced with prototype tools using the injection molding process.
- Injection molding simulation
- 3D printing
- Prototype tools
- Statistical design of experiments DoE
We ensure the consistent quality of our high-quality injection molding tools with our state-of-the-art toolmaking department. This offers us maximum flexibility in tool maintenance, spare parts production and even the complete construction of injection molds.
Toolmaking is supplemented by our special machine construction, in which product-specific production automation can be manufactured.
- CNC milling (high-speed milling with 5 axes)
- CNC erosion machines
- Wire erosion machine
- CNC automatic lathes
- Copy grinding machine
- Surface grinding machine
- Cylindrical grinding machine
(inside / outside) - Contour grinding machine
With our modern machinery of over 80 plastic injection molding machines, we process almost all thermoplastics into high-quality injection molded parts.
We have machines with clamping forces from 150kN to 5,500kN in single and multi-component technology at our disposal.
Immediate product finishing or testing can be carried out immediately using individual automation technology on the injection molding machine.
- Clamping forces from 150-5,500 kN
- Removal and packaging with fully automated robots
- Single and multi-component technology
- Inlay technique
- Fabric overmolding
- 100% inline testing
Depending on customer requirements, the degree of automation of product finishing can range from manual assembly to fully automated component assembly.
- Leak tests
- Ultrasonic and vibration welding
- Gluing
- Printing
- Heat sealing
- Proper storage
- Fast availability and reliable delivery
- EDI interfaces
- Labeling according to customer requirements
- 3500 m² storage capacity
- FiFo
- Consignment warehouse
- Just in time
- Just in Sequence
Our references
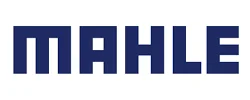
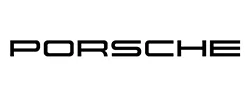
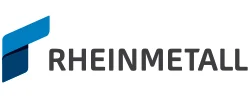
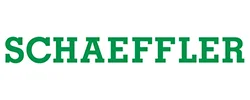
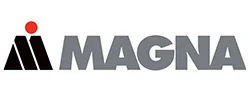
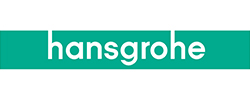
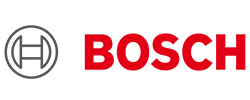